




Sluisweg 10 | 5145 PE Waalwijk | Netherlands +31 416 689 111
Contact us | stahl.com
We welcome your feedback and suggestions regarding this ESG report. Click here to share your input.
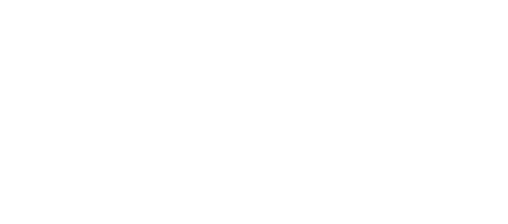
Stahl’s Global SHE Manager is responsible for defining our SHE strategy, standards and policies, and implementing them throughout the company, and ensuring compliance. Our employees are regularly consulted on SHE policy developments and evaluations through local works councils.
ISO 45001 certification
Employee survey and training
Safety culture and KPIs
TOPICS
Health and safety
ESG Roadmap topic
Remarks on 2023 achievement in relation to the target
Change
2022
2023
Unit
KPIs
Target
ESG issue
TRI = The total recorded injuries frequency rate is calculated as the number of total recorded number of injuries in the preceding 12 months over the total number of worked hours and referenced to a base of 1,000,000 h.
LTI = The lost-time injury frequency rate is the number of accidents involving the loss of one or more days of working time in the preceding 12 months over the total number of worked hours and referenced to a base of 1,000,000 h.
The severity rate is the number of lost working days due to injuries in the preceding 12 months over the total number of worked hours and referenced to a base of 1,000 h.
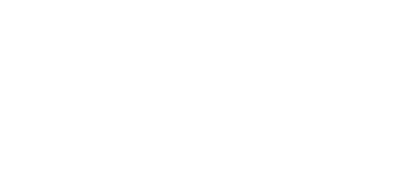
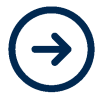
Back to top
Climate change threatens to have a significant impact on our business over the coming decades. We also recognise our own contribution to this critical issue, either directly through our production processes or indirectly through our wider value chain activities. By integrating our climate resilience plans into our core strategy, we believe we can secure our future and be a positive force for climate action in our industry.
The Stahl Climate Resilience and Adaptation Plan sets out our approach to climate risk mitigation, including our ambitious targets and how we plan to achieve them.
Taking action on climate change
Training
We require all employees to be trained in appropriate safety skills, with the understanding that safety is a mindset, not a department, and that everyone at Stahl is responsible for ensuring it. Each Stahl site has a training matrix that defines the knowledge required to perform each job. Operators working in production, as well as colleagues in laboratories, logistics, Centres of Excellence and offices, are trained according to their role and the risks involved.
Risk assessment
The Stahl Hazard Identification and Risk Assessment Methodology (SHIRAM) is our standard methodology for conducting safety risk assessments. This methodology has been designed to fit Stahl’s operations and processes and to integrate best practices for risk assessment and management. If our employees observe any additional hazardous conditions or behaviours, they are required to report them as part of our safety culture. When incidents occur, all Stahl sites are required to provide an investigation report. The methodology for this is defined at a local site level.
Stahl uses the ARA Platform, based on SHIRAM, to manage safety-related studies and share information between sites. In 2023, our focus was on increasing the usage of the tool at sites that were behind in their implementation journey. During the year, we also introduced a new template in the RA platform to map safety standards, identify gaps and define action plans for the tool’s implementation. We plan to further develop the templates in 2024.
Safeguarding the health and safety of our stakeholders
At Stahl, our responsibility for ensuring health and safety extends beyond our own workforce to our wider stakeholder base. Several webinars were broadcast to raise further awareness of these issues.
Certification
We demonstrate our continuous safety improvements through ISO certification. As part of our ESG Roadmap to 2030, we have set a target to ensure all Stahl manufacturing sites are ISO 45001-certified. In 2023, 64.6% of our total production volume came from ISO 45001-certified sites. ISO 45001, which replaces the previous standard, OHSAS 18001, requires companies to take a more proactive approach to safety, assessing and addressing hazards and risks before they cause accidents or injuries. In contrast, OHSAS 18001 takes a reactive approach, focusing on risks rather than solutions. In line with this change, we have updated our approach to be more proactive. Safety is also a key part of audits carried out by local authorities, with compliance necessary to receive certain permits.
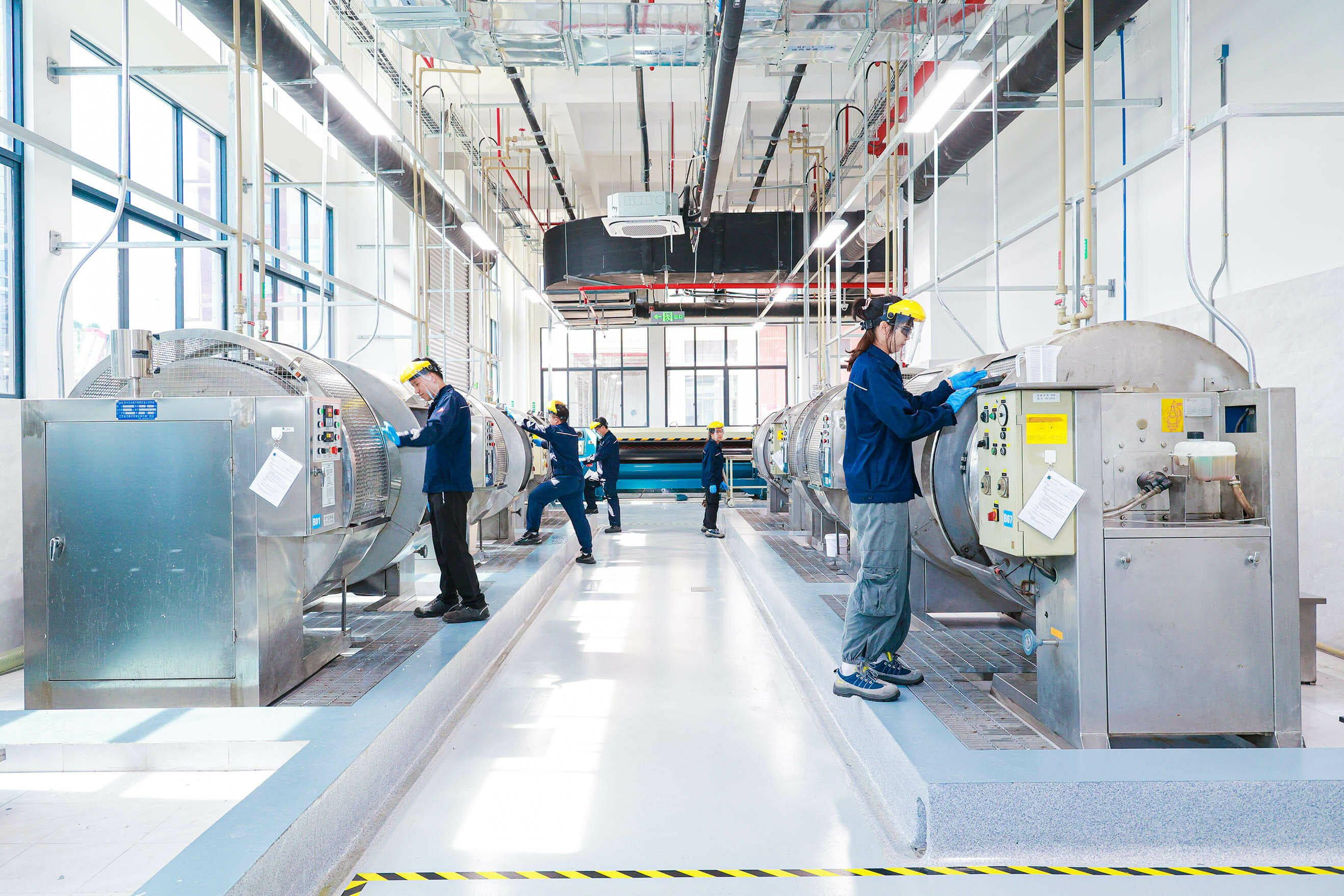
Stahl’s Global Safety, Health and Environment Policy
Monitoring our safety results
Certain leaders feel they do not have the power to solve issues or support their teams in taking action.
Employees do not always challenge managers’ decisions.
Some employees believe their managers do not hold all employees accountable to the same rules.
At some locations, supervisory and leadership skills could be improved.
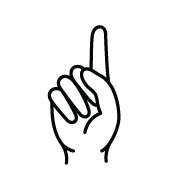
Stahl reports on its safety KPIs, both internally and to shareholders, every month. The reported metrics include injuries, incidents, audits, training, engineering projects and preventative measures.
In 2023, the rate of accidents and injuries decreased significantly, resulting in a decline in the total recorded injuries (TRI) frequency rate, lost-time injury (LTI) frequency rate and severity rate.
A strong safety culture involving the whole organisation;
Safety, health and the environment as top priorities;
Prioritising safety over short-term results;
Implementing industry best practices in addition to complying with all legal requirements; and
Knowledge as the basis of all decisions. Stahl will require employees to be trained in the skills necessary to carry out their duties and make decisions that help ensure safety.
A true safety culture is a mindset that prevails inside and outside the workplace;
A good safety record is never achieved through a large effort by a small group of people but by many small efforts from a large group of people;
The potential consequences of injuries at work mostly affect people and their social networks outside work; and
Stahl’s zero-tolerance policy on unsafe behaviour is designed to prevent injuries at work.
In 2021 and 2023, Stahl employees took part in a company-wide Organisational Cultural Diagnostic Instrument (OCDI) survey to help better understand our approach to safety as a company. The average response rate of about 98% reflects, in the first instance, our employees’ strong interest in safety. Performing two surveys in a short period of time helped confirm that the policies, principles and tangible actions that Stahl is putting in place are effectively shaping our shared culture in the direction of our vision and goals. The results of the second survey showed significant improvement in addressing many of the weak points highlighted in the initial survey. These results exceeded our initial targets for improvement, which were considered reasonable by external consultants.
The key takeaways from the OCDI surveys are as follows:
Our Global Safety, Health and Environment (SHE) Policy focuses on building a strong company-wide safety culture, with an emphasis on implementing industry best practices and complying with legal requirements.
The key principles of our SHE Policy are:
Stahl has dedicated policies in place to support our goal of zero injuries and accidents by 2030. Our health and safety policies apply to everyone who works at Stahl's locations, including temporary workers. Our broader focus on safety extends to our customers and neighbouring communities around our facilities.
In 2023, we introduced a new reporting system, Sphera HSM, to make safety reporting more efficient and consistent across Stahl’s different locations. In this way, we are able to anticipate and prevent accidents more effectively by identifying deviations and potential hazards before they cause significant issues.
In the first 10 months following the implementation of Sphera HSM, the number of observations and close calls reported across Stahl increased significantly, reaching approximately 250 reported events per million hours worked. From the data collected, assessment tools have been developed to set priorities on a consistent basis and define actions and investments.
Employees perceive an important improvement in the safety commitments by Stahl’s management.
Employees at all locations are mindful of safety and are encouraged to report any safety issues.
At many Stahl sites, employees appreciate the effort made by management to strengthen Stahl’s safety culture and the support they receive from the company. The progress Stahl has made in considering safety as a value further supports this.
At all sites, people help and support each other in creating a ‘family-like’ environment. Operators also discuss safety much more frequently.
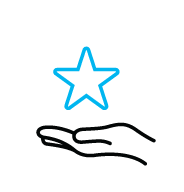
Ensuring the mental and physical well-being of all our stakeholders is an important foundation of Stahl's ESG approach. In this section, we explain how we ensure the safety of employees and contractors through training, policies, and certification; drive a culture of inclusion and diversity; and ensure fair and equitable labour practices throughout the supply chain. The occupational health and safety risks faced by Stahl employees include chemical contact and exposure to hazardous substances, chronic illnesses linked to chemical exposure, slips, trips and falls, and serious incidents.
Stahl’s ambition is to create a true safety culture, with a target of zero accidents and incidents. The Road to Zero (R20) programme has been developed to support this goal. The programme focuses on integrating safety into our company culture and ensuring all Stahl colleagues share the responsibility for safeguarding each other’s health and well-being. The key pillars of the programme are:





Sluisweg 10 | 5145 PE Waalwijk | Netherlands +31 416 689 111
Contact us | stahl.com
We welcome your feedback and suggestions regarding this ESG report. Click here to share your input.
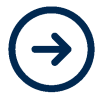
Back to top
Training
We require all employees to be trained in appropriate safety skills, with the understanding that safety is a mindset, not a department, and that everyone at Stahl is responsible for ensuring it. Each Stahl site has a training matrix that defines the knowledge required to perform each job. Operators working in production, as well as colleagues in laboratories, logistics, Centres of Excellence and offices, are trained according to their role and the risks involved.
Certification
We demonstrate our continuous safety improvements through ISO certification. As part of our ESG Roadmap to 2030, we have set a target to ensure all Stahl manufacturing sites are ISO 45001-certified. In 2023, 64.6% of our total production volume came from ISO 45001-certified sites. ISO 45001, which replaces the previous standard, OHSAS 18001, requires companies to take a more proactive approach to safety, assessing and addressing hazards and risks before they cause accidents or injuries. In contrast, OHSAS 18001 takes a reactive approach, focusing on risks rather than solutions. In line with this change, we have updated our approach to be more proactive. Safety is also a key part of audits carried out by local authorities, with compliance necessary to receive certain permits.
Risk assessment
The Stahl Hazard Identification and Risk Assessment Methodology (SHIRAM) is our standard methodology for conducting safety risk assessments. This methodology has been designed to fit Stahl’s operations and processes and to integrate best practices for risk assessment and management. If our employees observe any additional hazardous conditions or behaviours, they are required to report them as part of our safety culture. When incidents occur, all Stahl sites are required to provide an investigation report. The methodology for this is defined at a local site level.
Stahl uses the ARA Platform, based on SHIRAM, to manage safety-related studies and share information between sites. In 2023, our focus was on increasing the usage of the tool at sites that were behind in their implementation journey. During the year, we also introduced a new template in the RA platform to map safety standards, identify gaps and define action plans for the tool’s implementation. We plan to further develop the templates in 2024.
Stahl’s Global SHE Manager is responsible for defining our SHE strategy, standards and policies, and implementing them throughout the company, and ensuring compliance. Our employees are regularly consulted on SHE policy developments and evaluations through local works councils.
A strong safety culture involving the whole organisation;
Safety, health and the environment as top priorities;
Prioritising safety over short-term results;
Implementing industry best practices in addition to complying with all legal requirements; and
Knowledge as the basis of all decisions. Stahl will require employees to be trained in the skills necessary to carry out their duties and make decisions that help ensure safety.
Our Global Safety, Health and Environment (SHE) Policy focuses on building a strong company-wide safety culture, with an emphasis on implementing industry best practices and complying with legal requirements.
The key principles of our SHE Policy are:
Stahl’s Global Safety, Health and Environment Policy
Stahl has dedicated policies in place to support our goal of zero injuries and accidents by 2030. Our health and safety policies apply to everyone who works at Stahl's locations, including temporary workers. Our broader focus on safety extends to our customers and neighbouring communities around our facilities.
In 2023, we introduced a new reporting system, Sphera HSM, to make safety reporting more efficient and consistent across Stahl’s different locations. In this way, we are able to anticipate and prevent accidents more effectively by identifying deviations and potential hazards before they cause significant issues.
In the first 10 months following the implementation of Sphera HSM, the number of observations and close calls reported across Stahl increased significantly, reaching approximately 250 reported events per million hours worked. From the data collected, assessment tools have been developed to set priorities on a consistent basis and define actions and investments.
TRI = The total recorded injuries frequency rate is calculated as the number of total recorded number of injuries in the preceding 12 months over the total number of worked hours and referenced to a base of 1,000,000 h.
LTI = The lost-time injury frequency rate is the number of accidents involving the loss of one or more days of working time in the preceding 12 months over the total number of worked hours and referenced to a base of 1,000,000 h.
The severity rate is the number of lost working days due to injuries in the preceding 12 months over the total number of worked hours and referenced to a base of 1,000 h.
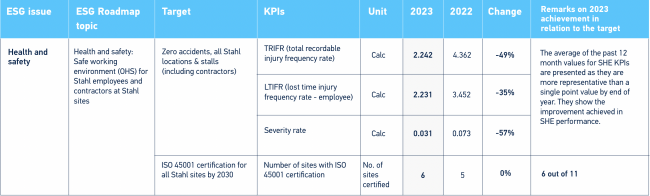
Stahl reports on its safety KPIs, both internally and to shareholders, every month. The reported metrics include injuries, incidents, audits, training, engineering projects and preventative measures.
In 2023, the rate of accidents and injuries decreased significantly, resulting in a decline in the total recorded injuries (TRI) frequency rate, lost-time injury (LTI) frequency rate and severity rate.
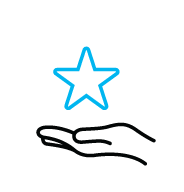
Employees perceive an important improvement in the safety commitments by Stahl’s management.
Employees at all locations are mindful of safety and are encouraged to report any safety issues.
At many Stahl sites, employees appreciate the effort made by management to strengthen Stahl’s safety culture and the support they receive from the company. The progress Stahl has made in considering safety as a value further supports this.
At all sites, people help and support each other in creating a ‘family-like’ environment. Operators also discuss safety much more frequently.
Monitoring our safety results
In 2021 and 2023, Stahl employees took part in a company-wide Organisational Cultural Diagnostic Instrument (OCDI) survey to help better understand our approach to safety as a company. The average response rate of about 98% reflects, in the first instance, our employees’ strong interest in safety. Performing two surveys in a short period of time helped confirm that the policies, principles and tangible actions that Stahl is putting in place are effectively shaping our shared culture in the direction of our vision and goals. The results of the second survey showed significant improvement in addressing many of the weak points highlighted in the initial survey. These results exceeded our initial targets for improvement, which were considered reasonable by external consultants.
The key takeaways from the OCDI surveys are as follows:
Stahl’s ambition is to create a true safety culture, with a target of zero accidents and incidents. The Road to Zero (R20) programme has been developed to support this goal. The programme focuses on integrating safety into our company culture and ensuring all Stahl colleagues share the responsibility for safeguarding each other’s health and well-being. The key pillars of the programme are:
A true safety culture is a mindset that prevails inside and outside the workplace;
A good safety record is never achieved through a large effort by a small group of people but by many small efforts from a large group of people;
The potential consequences of injuries at work mostly affect people and their social networks outside work; and
Stahl’s zero-tolerance policy on unsafe behaviour is designed to prevent injuries at work.
Ensuring the mental and physical well-being of all our stakeholders is an important foundation of Stahl's ESG approach. In this section, we explain how we ensure the safety of employees and contractors through training, policies, and certification; drive a culture of inclusion and diversity; and ensure fair and equitable labour practices throughout the supply chain. The occupational health and safety risks faced by Stahl employees include chemical contact and exposure to hazardous substances, chronic illnesses linked to chemical exposure, slips, trips and falls, and serious incidents.
ISO 45001 certification
Employee survey and training
Health and safety
TOPICS
Safety culture and KPIs
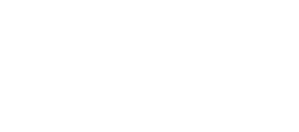
Certain leaders feel they do not have the power to solve issues or support their teams in taking action.
Employees do not always challenge managers’ decisions.
Some employees believe their managers do not hold all employees accountable to the same rules.
At some locations, supervisory and leadership skills could be improved.
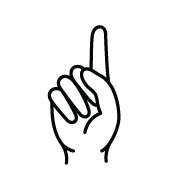
Safeguarding the health and safety of our stakeholders
At Stahl, our responsibility for ensuring health and safety extends beyond our own workforce to our wider stakeholder base. Several webinars were broadcast to raise further awareness of these issues.
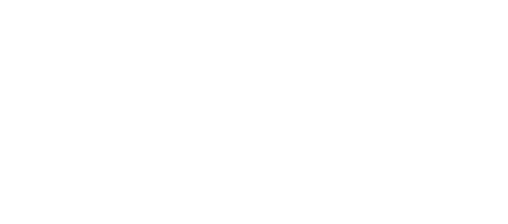
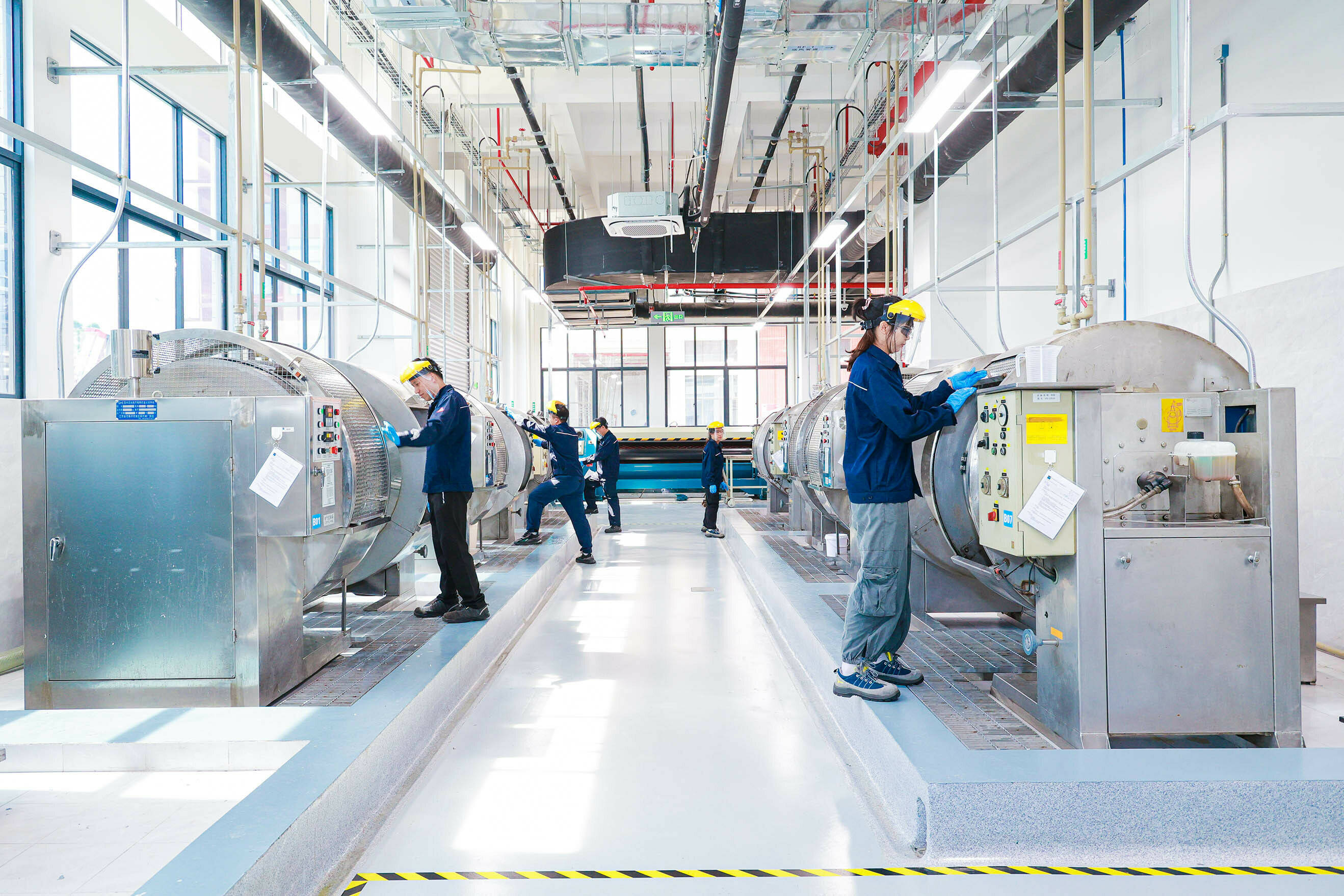